Hardware spraying electrophoresis line
-
Hardware spraying electrophoresis line
-
-
Electrophoretic coating is to immerse the object in a water-soluble paint as an anode (anode electrophoresis), and a corresponding cathode, which is connected with direct current between the two poles, and the paint is evenly coated by the physical and chemical action generated by the current. A coating technique on the object to be coated.
-
-
Electrophoretic coatings must use electrophoretic paints. Electrophoretic paints are often referred to as water-soluble paints. Electrophoretic paints and distilled water must be diluted in a certain ratio before they can be used. The seven components of the coating line mainly include: pre-treatment equipment, dusting system, painting equipment, oven, heat source system, electronic control system, suspension conveyor chain and so on.
-
-
Oven is one of the important equipment in the coating production line, and its temperature uniformity is an important indicator to ensure the quality of the coating. The heating methods of the oven are: radiation, hot air circulation and radiation + hot air circulation, etc. According to the production program, the single chamber and the pass type can be divided, and the equipment forms are straight-through type and bridge type. The hot air circulation oven has good heat preservation, uniform temperature inside the furnace and less heat loss. After testing, the temperature difference in the furnace is less than ±3oC, which is the performance index of similar products in advanced countries.
-
-
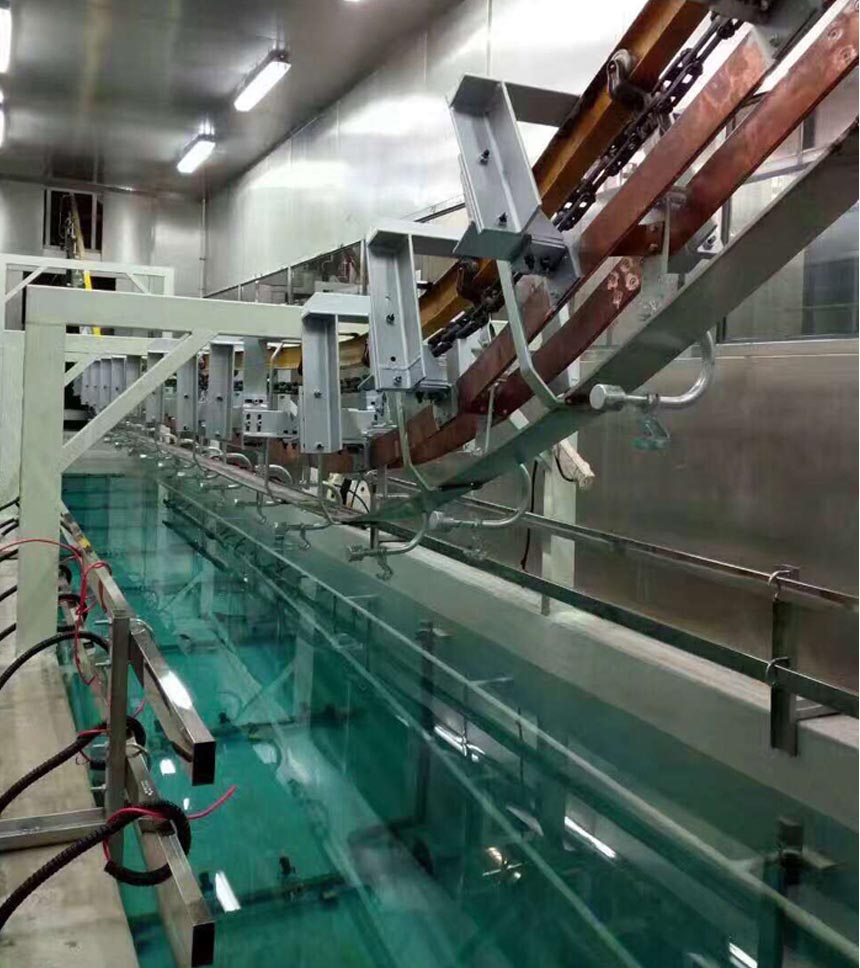
-
-
Electrophoretic coating generally consists of four simultaneous processes:
-
-
1. Electrophoresis: Under the action of a DC electric field, positive and negative charged colloidal particles move in a negative, positive direction, also known as swimming.
-
2. Electrolysis: The oxidation-reduction reaction is carried out on the electrodes, respectively, and oxidation and reduction phenomena are formed on the electrodes.
-
3. Electrodeposition: Due to electrophoresis, charged colloidal particles moving to the vicinity of the anode emit electrons in the template body, and are deposited in an insoluble state, and precipitated, and the paint film is formed at this time.
-
4. Electroosmosis: The phenomenon that the solid phase does not move and the liquid phase moves under the action of an electric field. The electroosmosis causes the water content in the paint film to be gradually discharged to the outside of the coating film, and finally forms a dense paint film which is almost incapable of passing current, has a very low water content, and has a relatively high electrical resistance.
-
-
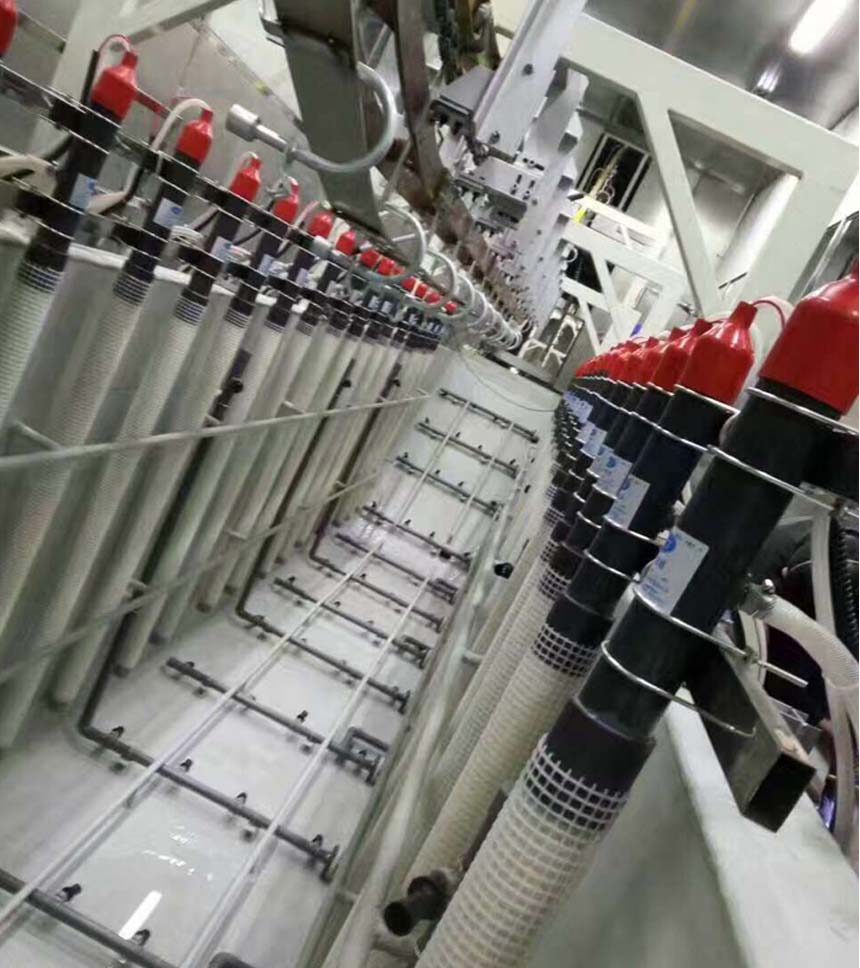
-
-
Spray electrophoresis - notes:
-
-
1. The coating production line should pay attention to the attachment of the coated objects. The test immersion method is used to design the hanging and the object on the painting production line in advance to ensure that the workpiece is in the best position during dip coating. The maximum plane of the object to be coated should be close to vertical, and the other planes should be at an angle of 10°-40° with the horizontal level, so that the painted surface of the residual paint can flow smoothly.
-
2. In the coating production line, in order to prevent the diffusion of solvent in the workshop and the dust falling into the paint tank, the dip tank should be protected.
-
3. After dip coating of large objects on the coating production line, the solvent should be basically evaporated before being sent to the drying room.
-
4. When painting, always pay attention to the determination of the viscosity of the coating. The viscosity should be measured 1-2 times per shift. If the viscosity increases by more than 10% of the original viscosity, the solvent should be added in time. When adding solvent, stop dip coating. After stirring evenly, the viscosity is measured and then the work is continued.
-
5. The thickness of the paint film is mainly determined by the rate at which the object is lifted on the coating line and the viscosity of the paint. After controlling the viscosity of the paint liquid according to the above requirements, the coating production line should determine the appropriate lifting rate according to the different equipment according to the maximum speed of the paint film of 30um. The object to be coated is uniformly raised at this rate. The lifting rate is fast, the paint film is thin, the lifting rate is slow, and the paint film is thick and uneven.
-
6. When the dip coating operation is performed on the coating line, the coating film on the upper and lower sides sometimes has a thickness difference, especially at the lower edge of the object to be coated. In order to improve the decorativeness of the coating, the excess accumulated paint drops can be manually removed by brush in small batch dip coating, and these paint drops can also be removed by centrifugal force or electrostatic attraction equipment.
-
7. When dip coating wooden parts on the coating line, pay attention to the time should not be too long, so as to avoid the wood inhaling excessive paint, causing slow drying and waste.
-
8. Strengthen ventilation equipment to prevent the danger of solvent vapor; pay attention to the arrangement of fire prevention measures and regularly check the coating production line.
-